401 East Washington, Springfield, Illinois
Commercial roofing
Commercial roofing project to replace a 7,500 sq.ft. roof with an EPDM roof installation at the Illinois Sheriff’s Association, 401 East Washington.
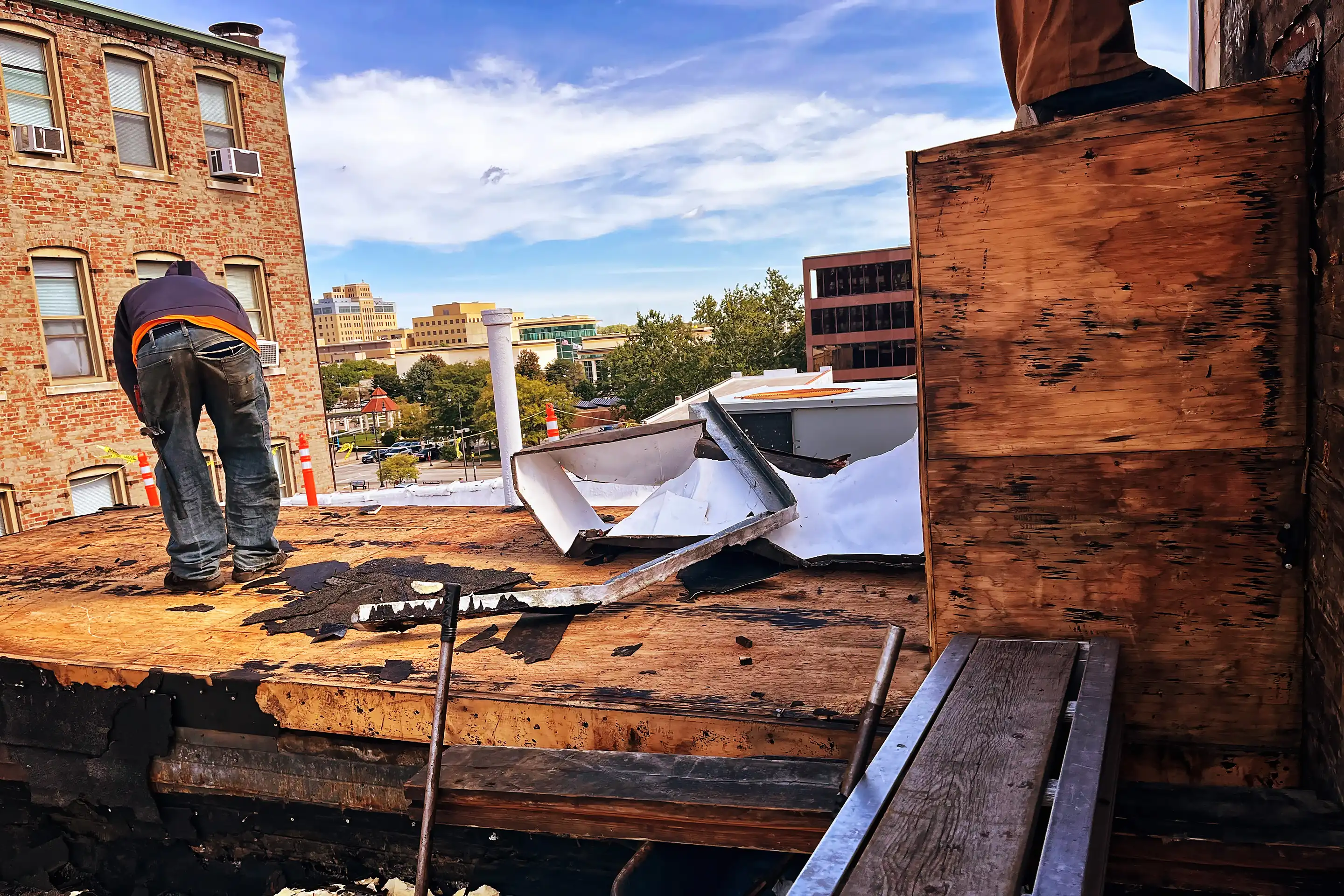
About this roofing project
We replaced a 7,500 sq. ft. roof on this commercial building at 401 East Washington. We completely removed the flat roof and decking material in sections, and installed new structural components, framing, plywood, and insulation board. We completed the installation of the new EPDM roof system in twelve days, utilizing a large project crew.
Setup
- The Green Monster dump trailer was delivered to the job site the day before the project start date. The parking location of the dump trailer (on the street near 401 East Washington) was reserved by permit with the City of Springfield.
- We ordered materials for delivery at 9:00 am on each day of the tear-off.
- The Equipter was used to protect windows, doors, and landscaping.
Materials
- ½” Insulation Board
- 3” Plates and Screws
- .060 EPDM Rubber Roofing
- RMS Strip
- DripEdge and Drip Batten
- EPDM Adhesive
- Pressure Sensitive Flashing
What's included in an EPDM roof replacement system?
EPDM rubber roofing is one of the best options for flat-roof commercial buildings. Short for ethylene propylene dienemonomer, this roofing system uses a single-ply membrane to protect a flat roof from leaks and other damage. If you want a commercial roof replacement that requires less maintenance than an old built-up roof, you should considerEPDM.
Benefits of EPDM roofing
EPDM has one of the longest life expectancies of any flat roofing. It is durable, eco-friendly, and even lowers your winter climate control costs.
While EPDM roofing is more expensive than other single-ply roofing systems, the roof will generally last twice as long, especially in hot weather. An EPDM rubber roof is more flexible than most roofing options, and it won't expand or contract as much with temperature changes, so roof maintenance is generally minimal. If it is damaged, there are plenty of options for patching and sealing the membrane, and a professional roofer like Blackhawk Roofing can make quick repairs.
How we install EPDM roofing
Single-ply roofing is installed using mechanical fasteners, a ballasted system, or fully adhered with chemical adhesive. Fully adhered installations offer the best leak resistance and the longest life expectancy, but they are also more complex. They require experience and skill to avoid common mistakes that can lead to roof failure.
1. Preparing the roof deck
The roof deck will be thoroughly cleaned to remove any oil or grime. We sand any protruding or sharp edges of the plywood or OSB board. Even a tiny amount of moisture can lead to problems with the adhesive, so everything must be dry before we begin your EPDM installation. We will cover your roof with clean, sanded plywood or OSB board to provide a barrier to protect the membrane. Installation is always according to the manufacturer's guidelines.
2. Add the drip edge and drip batten
Once the roof deck is ready, we'll install the drip batten into the fascia around the roof to extend the decking, which helps to guide drain water into the gutter system. Next, we'll install the drip edge, aligning the curved top with the batten. This will ensure that the water stays off the roof's edges and prevents erosion around your foundation.
3. Install the rubber membrane
We will need enough EPDM membrane to completely cover your roof, along with a thick overhang for the exterior walls and roof edge. We'll unroll the EPDM membrane and place it over the area where it will be installed. We will expose a portion of the roof decking under theEPDM and apply the bonding adhesive using a paint roller, leaving a 6" border around the edge. We'll attach the membrane while the adhesive is still wet by rolling it back into place. On hot days the adhesive will dry faster, so we may need to work with smaller areas at a time. Once the roof membrane is in place, we use a push broom to sweep out air bubbles and improve the bond. We'll continue rolling back the membrane and applying adhesive until all the roofing material is in place.
4. Apply the finishing touches
The final process takes time and expertise to do correctly. We'll apply adhesive to the border around the edge. Next, we'll seal the corners using pressure-sensitive flashing. We'll also use flashing to create watertight seals for vents and other mechanical items that penetrate the roof. Silicone sealant is used to seal all the edges to prevent moisture from entering the membrane. Finally, we remove excess membrane by trimming it.
Even the most straightforward roof repair jobs are best left to professionals, and a fully adhered EPDM roofing system is challenging for non-certified roofers to install correctly. We have the proper tools, experience, and certification to install your EPDM roof correctly and safely, without causing damage or leaving your roof vulnerable in the process.
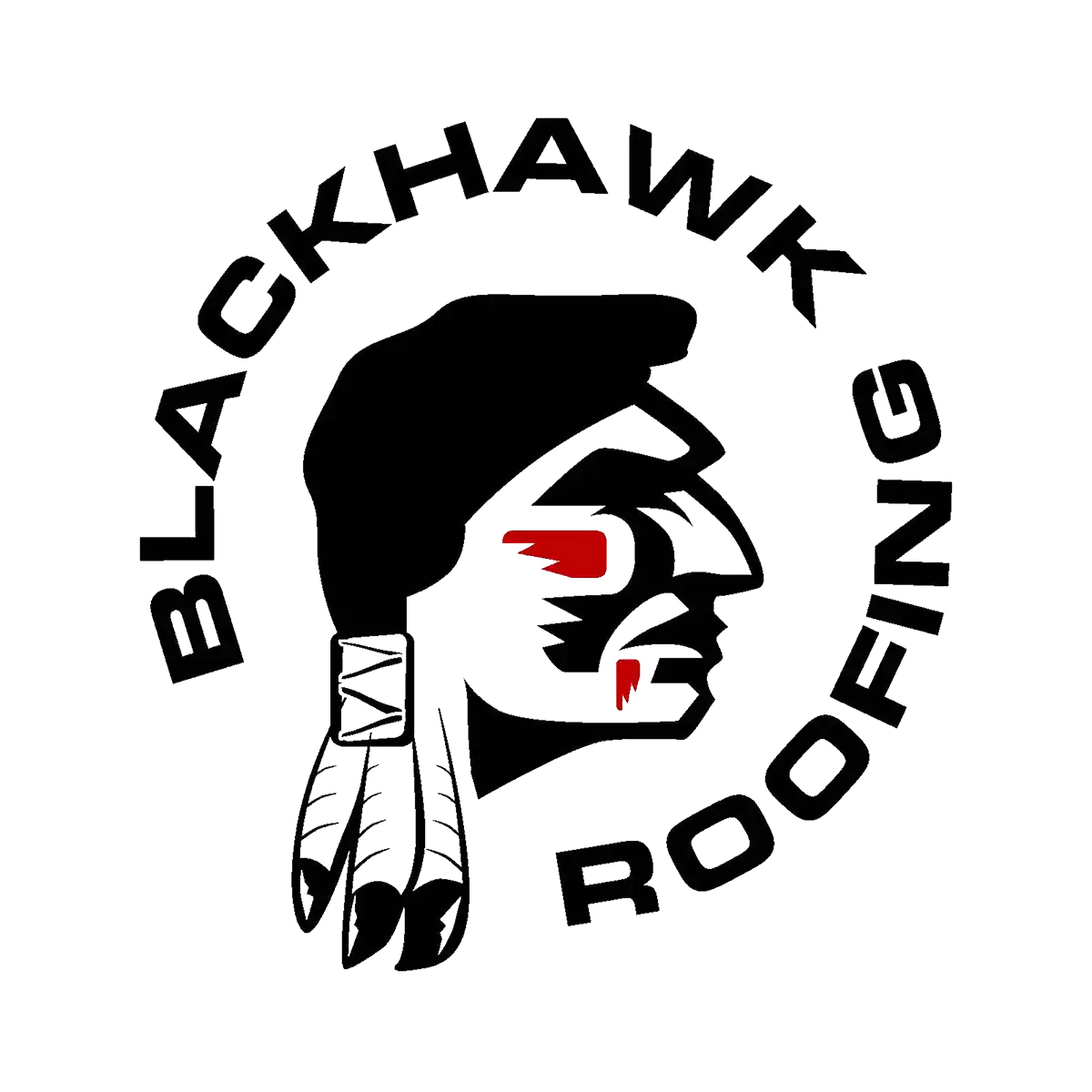