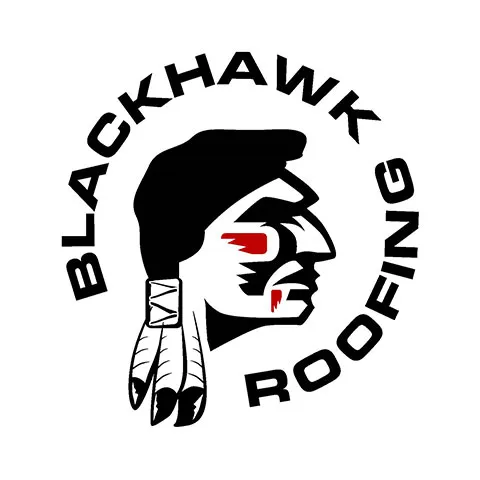
EPDM roofing technology
EPDM roofs are cost-effective, easy to install, and known for their exceptional hail resistance, UV stability, and weather resistance.
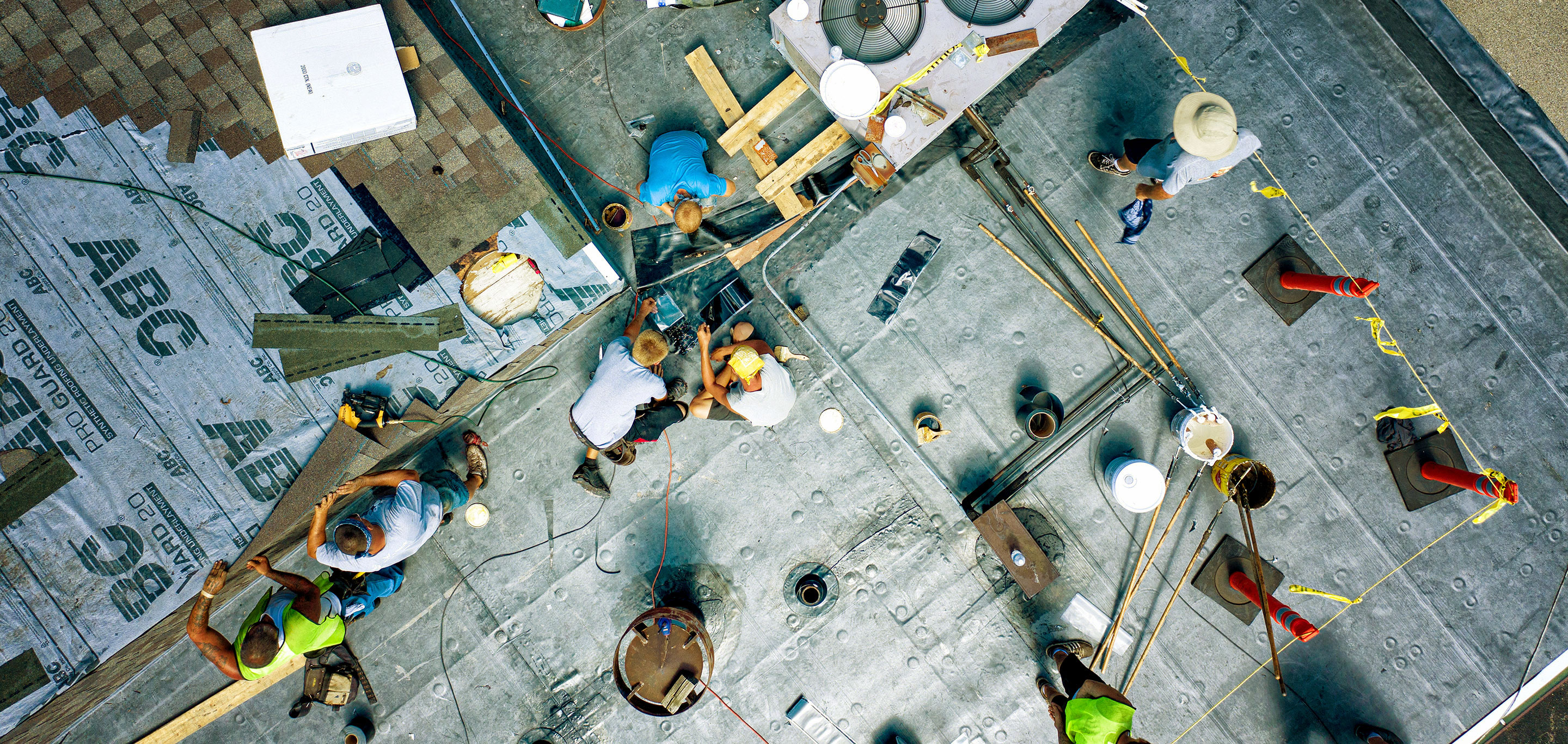
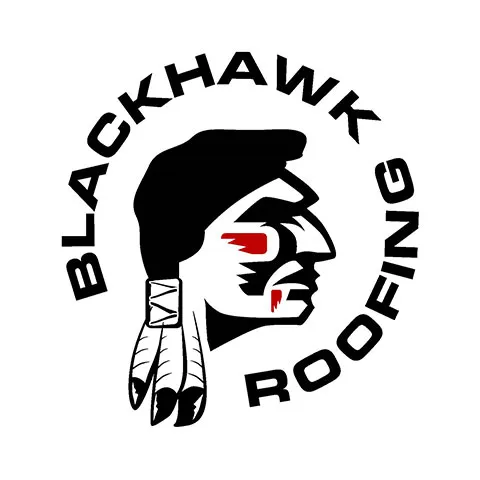
The evolution of EPDM roofing technology
First introduced in 1962, EPDM single-ply roofing membranes became increasingly popular in the 1970s as the Middle East oil embargo drove up the price of asphalt-based roofs and lowered the quality of available asphalt. EPDM was cost-effective and simple to install and quickly became known for its exceptional hail resistance, UV stability, and weathering resistance due to the ross-linked nature of its chemistry and the UV-absorbing power of its raw materials.
Since its introduction, numerous enhancements have been made to the system components, making today’s EPDM systems far more robust and of more excellent value than ever before. There are four main areas in which significant enhancements have been made to EPDM system technology, improving performance and increasing importance for the building owner.
Improvements to seams
The first area of improvement was in EPDM seaming technology. In the 1970s, EPDM seams were created using white gas and a Neoprene-based splicing adhesive. However, the Neoprene polymer in the splice cement could break down and lose strength with prolonged exposure to ponded water. While most systems are designed to promote positive drainage, it’s pretty common to have small areas of ponded water on the roof for extended periods. In the mid-1980s, a butyl-based splice adhesive was developed instead of white gas to clean the seam area. Butyl-based adhesives were used in pond liner applications and are very tolerant of ponded water. The seaming process still involved a few steps, leaving seams prone to variations caused by craft techniques and installation conditions.
It wasn’t for another 20 years that customized primers and double-sided seam tape emerged. These products dramatically simplified the seaming process and reduced craft inconsistencies—the more variability taken out of a process, the more consistent the results. Around 2005, seaming elevated to the next level with EPDM sheets and factory-applied tape, in which splice primer and splice tape are pre-applied to one side of the sheet in a factory-controlled environment. This breakthrough in technology further decreased craft issues. It improved the quality of finished splices because contractors simply had to roller-apply primer to one side of the sheet and then mate the two sheets together with a seam roller.
Factory-applied tape not only improved seaming productivity by 65 percent it also improved seam quality so dramatically that Carlisle Syntec saw an 80 percent drop inseam-related warranty claims. Today, contractors are reporting fewer call-backs for craft issues on EPDM seams than heat-welded seams.
Improvements to angle change securement
The methods for angle change securement of EPDM membranes have also improved significantly. In the early days, wood nailing strips were used to hold the membrane in place at a 90-degree angle at the base of parapet walls. The EPDM membrane is loose-laid in ballasted roofs, which were the most popular design back in the 1970s, leaving it free to move. All roofing membranes shrink slightly as they age, and in a ballasted system, the shrinkage force is transmitted to the perimeter securement. Wood nailing strips performed well when new, but over time, they would dry-rot and pull out over the fastener heads, causing the membrane to “bridge” away from the wall. Wood nailers were replaced with extruded rubber/plastic nailing strips that improved the weather-ability of the nailer itself. However, they still lacked enough fastener pull-through strength for some large ballasted jobs, and bridging remained an issue.
In 1989, Carlisle introduced the RUSS (Reinforcing Universal Securement Strip) detail, in which a 6” wide reinforced EPDM membrane is held in place by fasteners and 2” metal seam fastening plates. EPDM field membrane is then spliced onto the RUSS with the same shear-resistant products used for seaming.It took three years of solid marketing and education to convince contractors to change to this revolutionary new detail. However, it’s performed extraordinarily well over the past 27 years and is still used today.
Improvements to puncture resistance
EPDM roof membranes have grown in popularity over the years due to their increased puncture resistance. The most popular EPDM membrane-type was a 45 mil non-reinforced EPDM which provided excellent weathering performance with an economical price tag, but wasn’t as resistant to punctures as today’s 60 mil non-reinforced EPDM. In the mid 80s EPDM manufacturers introduced a reinforced EPDM sheet with an internal scrim added for additional toughness and durability, increasing the puncture resistance of EPDM by 50 percent on a 60 mil membrane. With this increase in protection comes trade-off compromises such as decreased heat weldability and reduced elongation due to the fixed reinforcement added inside, but overall EPDM roofs provide superior performance, strength and longevity. One trade-off with internally reinforced membranes of any type is that they contain less weathering material over the scrim. For example, on a 60-mil reinforced sheet, the thickness of the scrim ranges from 20- to 25-mils.
EPDM roofing was revolutionized when external reinforcement with fleece-backed EPDM was introduced in 1996. The puncture resistance of this 60-mil EPDM membrane increased by 300%, providing unparalleled protection from tears and other damage. Because the reinforcement is on the exterior, this EPDM also contains a full 60 mils of protective weathering material as well - double that of the original 45-mil EPDM! Because of this, contractors now have the option of 90-mil EPDM, which has the highest puncture resistance and most weathering material of any single-ply rubber membrane on the market.
Improvements to flashing details
Flashing details for EPDM roofing systems have steadily improved over the past 50 years, and these improvements have significantly enhanced the overall quality and performance of EPDM roofs. From 1962 to the 1980s, wall and penetration flashings were manufactured from uncured Neoprene. This material formed and spliced very well, but its UV resistance was less than that of the EPDM membrane. Over time, Neoprene flashing would crack and craze and became one of the prime modes of failure.
Flashing made of uncured EPDM was introduced in the mid-1980s. Uncured EPDM flashing offered dramatically improved weathering properties and none of the surface cracking issues. Then, a line of prefabricated pressure-sensitive inside/outside corners, pipe boots, and pourable sealer pockets for EPDM systems was developed. These products quickly gained popularity because they simplified the application process and improved the quality of the finished roofing system. Today’s pressure-sensitive flashings feature a complete 60-mil EPDM weathering layer laminated to 30-mil cured adhesive for a 90-mil total thickness.This added thickness contributes to the durability and robustness of EPDM flashings.
In 1992, wall and curb flashing details were updated to require cured (as opposed to uncured) EPDM membrane for added toughness, durability, UV resistance, and weather-ability. This was a natural progression with introducing the RUSS detail that allowed the high-performance EPDM field membrane to run continuously into the angle change and up the wall.
Today’s EPDM systems are time-tested and built to last, and are very much in sync with the growing emphasis on sustainable construction. EPDM has earned an excellent reputation for weather-ability, hail resistance, and long-term value from over 50 years of real-world performance. Technological advancements such as seam tapes, primers, RUSS angle change securement, puncture-resistant membrane options, and more robust flashing details have made EPDM the system of choice for countless architects, contractors, and building owners.
Blackhawk Roofing has built replacement roofs for thousands of residential and commercial customers in Springfield and Central Illinois. We've also done many hundreds of roof repairs. Blackhawk Roofing provides outstanding value on every project. Call owner Dan Schnell at 217-741-6251 to request a Free Estimate.
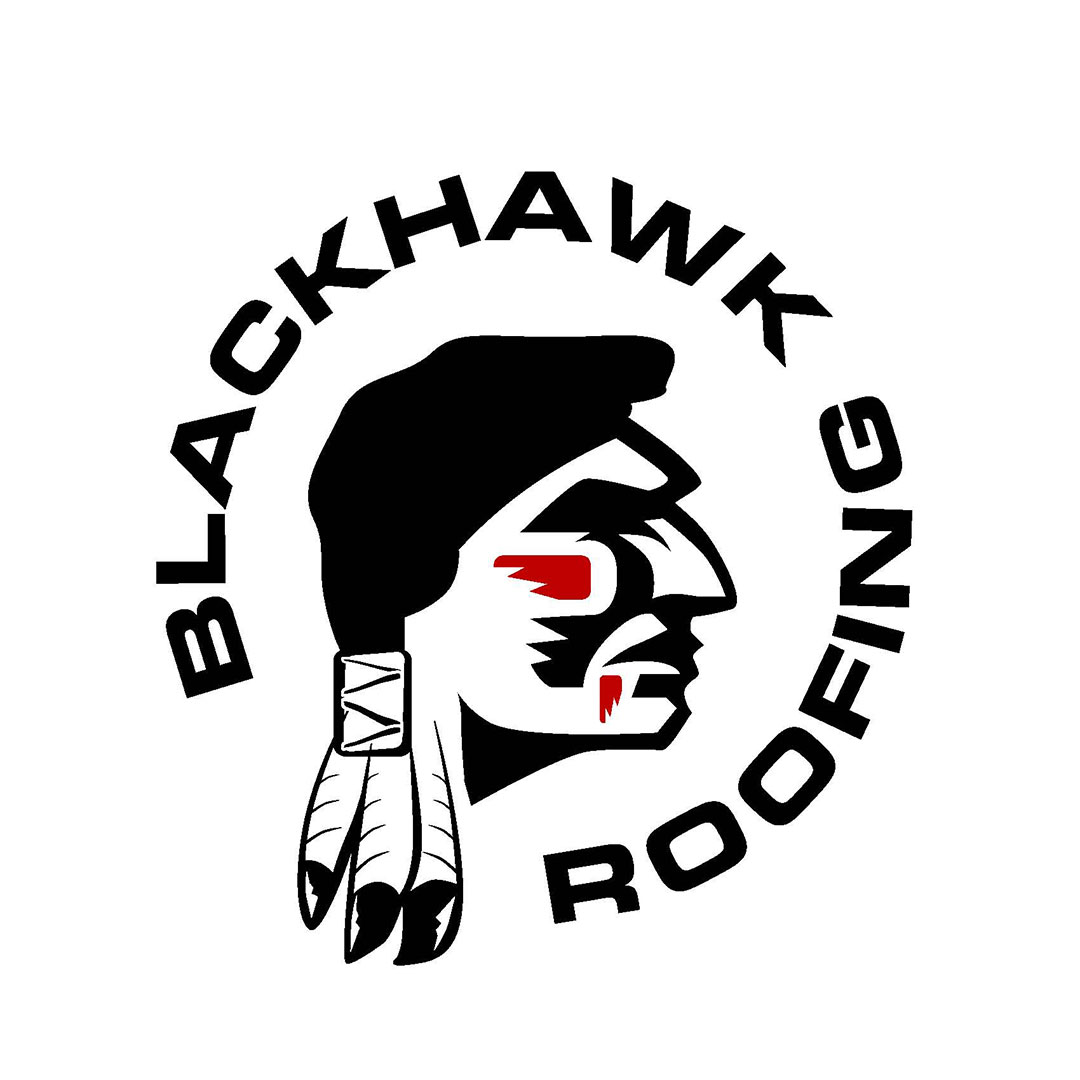
Licensed Roofing Contractor
Blackhawk Roofing is a licensed, certified, and insured roofing contractor. We specialize in residential roofing and EPDM commercial roofing. We have repaired or replaced thousands of old and damaged roofs in Springfield and Central Illinois.